You've probably been told that it's alright to make a mistake as long as you learn from it. This is something we preach here at East West. While mistakes do happen, some can be very costly and chip away at your bottom line (something our CFO likes to avoid). One such example is accumulating costs from rework, which is the correcting of a defective, failed, or non-confirming item during or after inspection. Essentially, this means lost time, increased waste and unplanned costs! Learning how to minimize this will eliminate negative effects and lead to cost savings and the production of higher quality products overall.
Common Causes of Rework
Let's talk a bit about how the need for reworking crops up as an issue in the first place. Obviously a product will need additional work because something is defective or otherwise inefficient. Below are a few common mistakes or happenings that could lead to a need for product modification:
- Wrong item ordered
- Machine malfunction or human error
- Design change not communicated (at all or in a timely manner)
- Design change not implemented properly
- Product damaged in transit
- Product damaged in use
5 Ways to Reduce Rework Costs
Now let's take a look at five ways you can cut back on reworking and associated costs to protect your bottom line and improve efficiency and quality across the supply chain.1. Maintain well organized filing systems
Long gone are the days of hard copies and manila file folders. Well, maybe not completely, but you should definitely have hard copies backed up digitally. And even then, it's not quite good enough. Invest in more sophisticated digital software and filing systems to manage your CAD drawings, bills of materials (BOMs) and standard operating procedures (SOPs). Track revisions to ensure your employees are referencing the most up-to-date, accurate information at all times. Biting the bullet and investing in project management programs will reduce the risk of ordering incorrect components or building to an old revision level (bad news for both you AND your customers).
2. Prioritize open communication
If you are working with a contract manfacturer, communicate design changes to your CM immediately. Give them a heads up since a change can seriously disrupt production if not handled properly. If you are making a major revision, it could affect the flow of production, required training, scheduling and total cost, among other factors. Remember: If your CM works with additional suppliers, they will need time to communicate the changes to those suppliers as well.
If at all possible, avoid making major design changes in the middle of a production run. Instead, wait until the next order for full implementaton to ensure the change is adequately planned and executed. This will also make the product revision levels easier to track for you, the supplier and your customers.
3. Always be proactive
Taking a proactive rather than a reactive stance helps control quality issues. Holding regular factory inspections will identify problems and opportunities to improve processes. The key is to identify the source of an issue (using the 5 Whys and Root Cause Analysis) and resolve it at the most basic level (new equipment or fixtures, better trained workers, upgraded software, etc.) In the case of major deficiencies, advanced technologies are probably worth the capital investment.
A good example of being proactive is emphasizing product design early on and sorting out kinks in the sampling phase. The more fine-tuned a product design is pre-production, the less risk of complications down the road. Once the item is manufactured, you aren't off the hook just yet. Properly packaging and handling goods reduces the risk of in-transit damage, which could lead to return merchandise authorizations (RMAs) and the likelihood of repairing or scrapping materials.
Lastly, don't take training lightly! Well trained employees will deliver better work, guaranteed. Skimping on training may save you time in the beginning, but it will lead to a higher chance of error in the long run. And you know what that means....
4. Implement quality control procedures
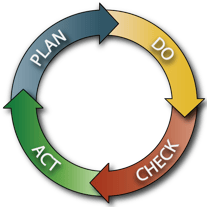
A sophisticated and highly regulated quality control procedure is vital to minimizing costs. Adopting a Total Quality Management (TQM) philosophy and implementing the PDCA Cycle or another closed loop, continuous improvement system is a great jumping off point. Aim for Six Sigma quality and lean manufacturing practices to eliminate waste and improve quality as much as possible. If you do not already do so, launch a Corrective and Preventive Action (CAPA) program to diagnose an issue using the 8D process, assign a team to address it, and resolve it within a specified timeframe. This process has proved successful here at East West and has enabled us to reach a quality failure rate of only 90 parts per million (PPM) in 2015 YTD.
5. Develop a plan for scrap materials
Repairing or altering a product should always be prioritized over scrapping, but sometimes scrap is unavoidable. In this instance, you should aim to reduce the amount of waste as much as possible. Determine if the product itself or individual components can be refurbished and repurposed. Perhaps there are plastic parts that can be recycled. Getting creative and avoiding scrapping can help you dodge hefty dumping fees, depending on the specific material and your location.
Did you find this post useful? Check these out too!